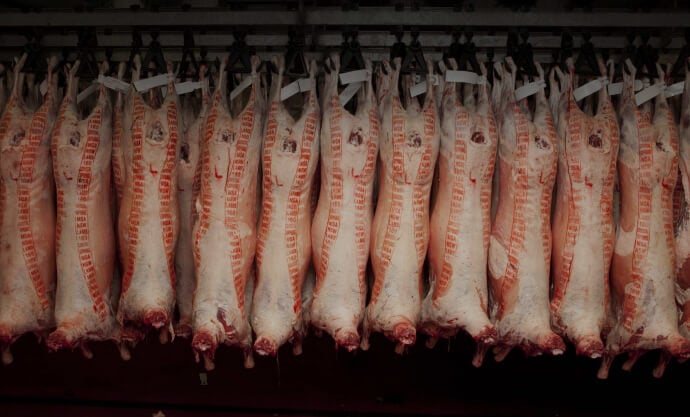
PRODUCTION
Preparation
After processing, and depending on the market destination, a carcase is then further prepared and processed to prepare it for consumption.
Hanging
Once a carcase is dressed (the head, feet, hide and internal organs removed), it is then hung for around 24 hours until it is the right temperature to be broken down into the basic cuts.
The way the carcase is hung impacts on the quality of the end product, so it’s critical that it’s done properly. There are two methods regularly used – tenderstretch and Achilles tendon.
Hanging Methods
Tenderstretch
The most common method is to position the hanging hook under the ligament that runs down the back of the carcase, or under the hip-bone of the pelvis. In this position, the legs are suspended at a 90° angle, which limits the contraction of muscles during rigor mortis. This method especially benefits the hindquarter cuts.
Achilles
In the more traditional Achilles technique, the hanging hook is positioned through the rear heels. Gravity causes tension in these muscles as the carcase goes through rigor mortis which can result in slightly tougher meat than tenderstretch method.
Ageing
During the ageing process, proteins that give muscles form and functionality start to be broken down by enzymes left in the body after slaughter. As these larger proteins disassemble into smaller ones, meat becomes tenderer.
There are two key types of ageing meat - wet ageing and dry ageing – whilst both processes assist in the tenderisation of meat; dry ageing also results in a change in the flavour and texture of the meat. Ageing does nothing to tenderise heavy connective tissue in meat – this is combated by slow moist cooking or acidic marinades.

Wet Ageing
Wet Ageing
Wet ageing is a general storage process that occurs after a carcase is broken down or boned when meat is vacuum packaged and stored. Wet ageing enhances tenderness, but does not greatly influence the flavour of the meat. It is popular because it requires less time and space than dry ageing meat, plus there is no weight loss as moisture is retained in the meat.
The Process
Endogenous proteolytic enzymes weaken the structural myofibrillar proteins in the meat. This takes 10 to 14 days and results in a more tender meat. Meat is aged in its own blood and serum therefore growth of Lactobacilli can result in a more subtle flavour compared to dry aged meat.
Temperature Control
A storage temperature below 5°C must be used. Frozen or thawed meat must not be aged because the desired enzymatic action will not occur and mould growth will not be initiated on the surface of the meat.
Dry Ageing
Dry Ageing
Despite its current popularity, dry ageing isn’t a new technique or trend. Until the developments in chilling and vacuum packing in the early 1960s, dry ageing was the most common, and often, the only way to prepare meat for storage and transport. The process of dry ageing was traditionally carried out by hanging either the whole carcase or cut pieces of the carcase in a cool room.
The secret to dry aged meat is the reduction in moisture. Techniques in dry ageing can vary depending on the desired flavour outcome and the amount of the moisture that is lost. The process is typically 7-14 days but can be up to a month or longer. During this time, a protective crust of bacteria forms over the meat which helps to concentrate flavour. This crust is then removed before the meat can be safely prepared and served to customers. Dry Ageing is not an exact science, but one that requires an understanding of how elements work together to impact flavour development, shelf life, product shrinkage and loss due to spoilage. Dry aged meat should be stored at around -0.5 o C to 3 o C, with humidity set between 75% and 85%. Dry ageing can result in losing up to 8.5% of yield, but what’s lost in bulk is made up for in flavour. During the process, fats become aromatic as left over energy in the muscle turns into glucose, which enhances the flavour.